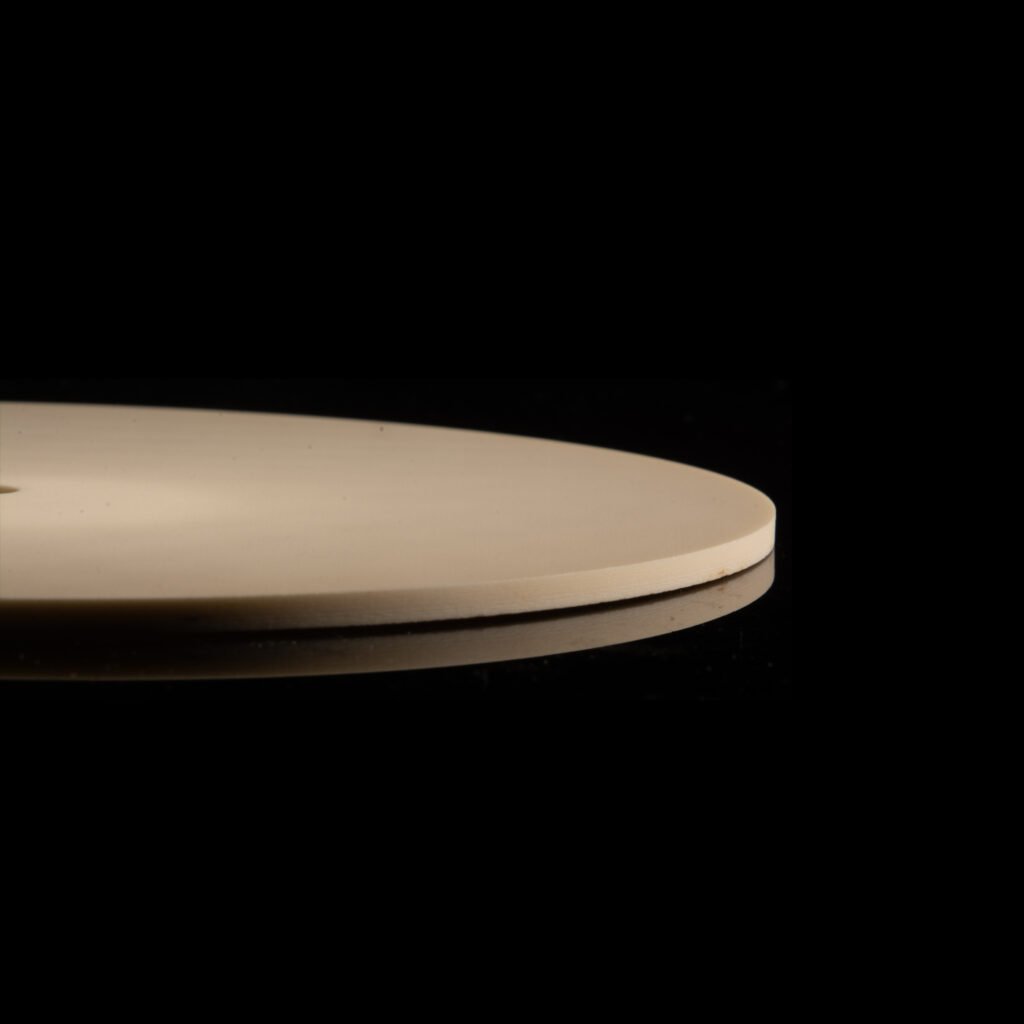
氧化铝陶瓷(Al₂O₃陶瓷)因其优异的高温稳定性、机械强度、耐腐蚀性和绝缘性能,被广泛应用于电子、机械、化工、航空航天等领域。成型工艺作为氧化铝陶瓷制备的核心环节,直接影响材料的微观结构及最终性能。本文将系统解析氧化铝陶瓷的主要成型方法、工艺参数控制及质量控制要点。
一、氧化铝陶瓷成型工艺概述
氧化铝陶瓷成型是将高纯度氧化铝粉体通过特定工艺制成预定形状坯体的过程,其核心目标在于实现坯体的高致密性、均匀性和尺寸精度。目前主流的成型工艺包括干压成型、等静压成型、注浆成型、注射成型和流延成型等,不同工艺适用于不同应用场景。
1. 干压成型(Dry Pressing)
原理:将造粒后的氧化铝粉体填充至金属模具中,通过单向或双向机械压力(通常为50-200 MPa)压实成型。
优势:设备简单、效率高,适合批量生产简单形状的陶瓷部件(如基板、衬套)。
局限:坯体密度分布不均匀,易出现层状裂纹,难以制备复杂结构。
2. 等静压成型(Isostatic Pressing)
原理:利用液体或气体作为压力传递介质,对密封模具中的粉体施加各向同性压力(可达300 MPa以上)。
分类:冷等静压(CIP)与热等静压(HIP)。
特点:坯体密度均匀、缺陷少,适合制备高性能大型构件,但设备成本较高。
3. 注浆成型(Slip Casting)
原理:将氧化铝浆料注入多孔石膏模具中,通过毛细作用脱水形成坯体。
工艺改进:压力注浆和真空注浆可缩短成型周期至数小时。
应用:适用于薄壁、异形件(如坩埚、绝缘套管)。
4. 注射成型(Injection Molding)
流程:将氧化铝粉体与热塑性粘结剂混合造粒,在注塑机中加热至150-200℃注入模具,脱脂后烧结。
优势:可制备复杂三维结构微型零件(如光纤连接器),尺寸精度达±0.1%。
挑战:脱脂工艺需精确控制升温速率以避免开裂。
5. 流延成型(Tape Casting)
工艺:将含有机溶剂的氧化铝浆料通过刮刀在基带上形成厚度10-500 μm的薄膜,干燥后层压成型。
核心应用:多层陶瓷电容器(MLCC)、电子封装基板。
二、成型工艺的关键技术参数
1. 粉体特性控制
粒径分布:D50控制在0.5-1.5 μm可优化填充密度,粒径过粗易导致烧结收缩不均。
比表面积:通常要求5-15 m²/g,过高会增加浆料粘度。
造粒工艺:喷雾造粒可获得流动性良好的球形颗粒,松装密度达1.2-1.8 g/cm³。
2. 成型压力与保压时间
干压成型压力需根据坯体厚度调整:厚度<5 mm时采用100-150 MPa,>10 mm时需降低压力避免弹性后效。
等静压保压时间一般为2-5分钟,确保应力充分释放。
3. 粘结剂与润滑剂体系
常用粘结剂:PVA(聚乙烯醇)、PVB(聚乙烯醇缩丁醛),添加量1-5%。
润滑剂选择:硬脂酸锌或石蜡可减少模具磨损,添加量0.5-1.5%。
4. 模具设计优化
干压模具需设置0.5-1°脱模斜度,型腔表面粗糙度Ra<0.4 μm。
注浆成型石膏模具孔隙率应控制在30-40%,孔隙直径2-5 μm。
三、成型过程中的质量控制
1. 常见缺陷及解决方案
分层现象:由粉体含水率不均或压力释放过快引起,可通过预压排气(2-3次)改善。
边缘裂纹:模具设计不良导致应力集中,需优化圆角半径(R>0.3 mm)。
密度梯度:采用双向加压或等静压工艺可使密度偏差<1%。
尺寸超差:烧结收缩率预测模型误差应控制在±0.5%以内。
2. 检测方法
坯体密度:阿基米德法测量,要求相对密度≥55%。
缺陷检测:工业CT扫描可识别50 μm以上的内部裂纹。
尺寸精度:三坐标测量仪(CMM)检测关键尺寸公差。
四、应用领域与技术发展趋势
1. 典型应用场景
电子领域:96%氧化铝基板(热导率24 W/m·K)用于LED散热。
机械密封:99.5%氧化陶瓷环,硬度达Hv1600,耐磨损寿命提升3倍。
生物医疗:多孔氧化铝骨修复支架(孔隙率60-70%)。
2. 技术发展方向
增材制造:光固化(DLP)成型氧化铝陶瓷,可实现100 μm级精细结构。
智能化控制:基于机器学习的压力-密度实时反馈系统。
绿色制造:水基流延体系替代有机溶剂,降低VOC排放。